Announcing the 2021 P.I. Process Instrumentation Innovation Awards winner and honorable mentions
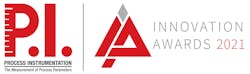
For more than 20 years, P.I. Process Instrumentation’s annual Innovation Awards program has recognized the latest solutions in fluid and gas handling applications. The program accepts nominations from companies that would like to submit their technology breakthroughs in process instrumentation, and the winners are determined by a reader voting process.
We would like to thank everyone who participated in the awards program by nominating or voting. And, congratulations to the winner and honorees. We hope to see your solution nominated next year.
The following case studies highlight the technology solutions from the 2021 Innovation Awards winner and honorable mentions.
WINNER: Swagelok Gas Distribution Program
Swagelok Company
200 gas lines — One comprehensive solution
Since many of these gases can pose significant risks to workers if they are not properly contained, the importance of leak-tight gas distribution systems is paramount. Over time, the gas distribution systems had become more complex, with a multitude of components from several different manufacturers being used in one system. There was also a big push to improve safety — again due to the age of the site and how much the gas distribution system had been changed and modified. In addition, the company needed to find ways to reduce its gas panel replacement and maintenance costs. In the United Kingdom, components are date-stamped, and guidelines suggest that they be replaced every five years or based on the manufacturer’s recommendation. On average, that meant the company had to replace at least 10% of its gas panels each year at an estimated cost of $52,000 (£40,000) per year.
The company needed to streamline its systems and improve efficiencies — all with a focus on health and safety — and sought help from a trusted source that could help make that happen quickly and efficiently.
The solution
Advisers identified opportunities to standardize gas panel design throughout the system (Figure 1), and Swagelok source inlets and gas panels were installed to establish reliable connection points between high-pressure source gases and the rest of the distribution system. The chemical company took advantage of standardized, configurable gas delivery systems from Swagelok (Figure 2) to quickly replace its gas distribution panels and keep its gas lines up and running.
New designs incorporated dedicated lines for safer purging, offered easier access to critical relief valves, enabled easier maintenance, and included a common panel footprint for improved workflow.
The results
In addition, the gas distribution panels became a useful tool that not only saved the company money and improved the safety of its workers but also made the jobs of the company’s two gas line engineer overseers easier and less stressful. Now, with simplified maintenance responsibilities, those engineers are able to focus their attention on other tasks — as the gas distribution system is not their only job function, saving the customer additional money in the long run.
Unlike those manufactured by other companies, Swagelok gas panels can be easily repaired instead of being replaced every five years, allowing the chemical company to save more than $52,000 (£40,000) every year (based on a 10% annual replacement rate with the old panels). Finally, the company reduced its carbon footprint, as leaks were reduced and replacements became less frequent.
HONORABLE MENTION: Centurion Guided Radar (CGR) Interface Level Transmitter
Hawk Measurement
PoE level transmitter increases business efficiencies at a major US cattle feed company
HAWK’s CGR PoE units work to control inventory and have drastically cut costs for the livestock feed company, ranging from reducing installation costs to maximizing production efficiencies that result in large cost savings throughout the supply chain. By implementing PoE with AI, personnel can access real-time data on process measurements and machine function from their PC, tablet or smartphone. The cattle feed company also receives detailed reports that inform operations how their process is performing — in real time and over time.
The CGR PoE system also informs accounting and administration with important cost accounting detail, when to purchase and what to purchase, and it tracks commodity trading with inventory availability. The AI components will make predictions as to when a breakdown is likely to happen, allowing maintenance to plan a scheduled outage versus the inevitable costly emergency shutdown.
Another benefit of utilizing HAWK’s PoE remote monitoring is that personnel can monitor and troubleshoot issues from any location, at any time, often resolving the situation before they reach a breakdown state. Complete diagnostics and system configuration can be accomplished from plant-resourced engineers and maintenance personnel to factory-trained developers and technicians, all without entering the plant site or location.
An ongoing issue with globally owned and operated companies is the necessity to make decisions on a broad range of issues at a moment’s notice. Energy issues, weather-related issues, raw material and supply chain issues, health and safety issues as well as cost and accounting issues are ever-increasing concerns that require real, accessible data and analytics. The lack of visibility into daily processes will cause increasing problems with high-compliance industries such as food, energy and transportation. The cattle feed company recognized its need for an automated process solution and purchased hundreds of HAWK’s CGR PoE systems to mitigate these concerns and to increase business efficiencies. They have been so satisfied with the results that they are planning to implement many more systems company-wide.
HONORABLE MENTION: Bedrock OSA +Flow
Bedrock Automation
Securing flow measurement and control in pipeline operations
Some facilities only monitored inputs and executed automatic and remote control of valves and other equipment. Other sites, however, required natural gas custody transfer measurement, automatically executed station controls and data concentration for third-party equipment.
Both types of locations required a control and measurement platform with built-in security and the ability to communicate with SCADA systems and local HMIs across modern, open and secure communications protocols.
One option was to use a PLC for the control function and a flow computer for the natural gas custody transfer measurement. However, the separate PLC and flow computer at the metering locations dramatically increased the complexity of the design, decreased reliability, and increased the life-cycle cost. Not only that, but there was no combination of vendors, hardware and software that could provide intrinsic security and support for modern, open protocols using separate PLCs and flow computers. This option required adding additional hardware to secure the product and gateways to provide protocol support. Such a solution would not have been scalable or sustainable.
The pipeline operator evaluated the Bedrock OSA platform and determined that it met all criteria of the project. The Bedrock OSA +Flow performs custody transfer measurement of natural gas and petroleum and executes DCS level controls at PLC speeds. The OSA +Flow supports secure MQTT and OPC UA right out of the box, with no additional hardware or software licensing required.
Because the Bedrock OSA +Flow is intrinsically secure, there is no requirement to add hardware and software to protect it from cyber threats. The OSA +Flow was designed to be secure from the ground up, so authentication and encryption are built in. Cyber protection does not need to be bolted on after the fact.
One of the most important ways that implementing an intrinsically secure control and measurement solution reduces life-cycle costs is enabling use of open standard applications and tools. Configuring secure applications with Bedrock OSA +Flow can be done with the IEC 61131 programming environment that Bedrock supplies for unlimited free use. The pipeline operator will be able to easily port over most of their control algorithms from their existing system and, going forward, will have access to an entire community of resources using this open programming standard, reduce operating costs and optimize operations.
HONORABLE MENTION: High Pressure Coriolis Flow Meter
Emerson Electric - Micro Motion
High Pressure Coriolis Flow Meter helps hydrogen refueling station
For accurate measurement, TotalEnergies Gas Mobility decided to install Emerson's Micro Motion High Pressure Coriolis Flow Meters on hydrogen dispensers. These dispensers can fill vehicles with hydrogen at 350 and 700 bar operating pressure conditions for transportation and private vehicles respectively. Micro Motion HPC015 Coriolis Flow Meters are designed specifically to handle maximum operating pressure up to 1060 bar. It helps to ensure transfer of high-pressure fuels like hydrogen.
"The Flow Meter in the dispenser measures the hydrogen mass that has gone through,” said Arthur van ‘t Wel, technical support engineer of TotalEnergies Gas Mobility. “This is certified by national and OIML-139 standards that states that every amount that has gone through the certified meter, has actually gone through it. Together with the payment system and calculator that are also certified and tested, it assures the measured quantity and billed amount are within the set limits.”
The 350 and 700 bar hydrogen (H2) dispensers used at the TotalEnergies’ hydrogen refueling station in Arnhem were the first to be calibrated and certified by the Netherlands Measurement Institute (NMi) and the National Measurement Institute of the Netherlands (VSL). Thus, vehicles that fill up at this TotalEnergies station under the PitPoint brand receive full transparency and certainty about the amount of hydrogen.
Emerson's Micro Motion High Pressure Coriolis Flow Meter is easily integrated with a small meter body and large range of transmitters, making it suitable for high measurement accuracy for hydrogen gas flow. A safe meter design includes built-in rupture disk for ultra-high pressure environment up to 1060 bar in accordance with ASME B31.3 Process piping code.
HONORABLE MENTION: Proline t-mass F/I 300/500
Endress+Hauser
Bidirectional sensor distinguishes between flow direction, improving internal accounting
- Assigns consumption to the wrong consumers.
- Delivers false information.
- Misrepresents gas consumption patterns within a plant.
T-mass 300/500 is the first bidirectional sensor that can distinguish between flow direction and both measure and totalize flow in both directions. This improves internal accounting and eliminates false reporting.
Air measurement at biotech company
A rooftop pipe is used for air delivery to a combustion process of a boiler and for exhausting air mixed with small amounts of vapors in over-pressure situations from another process. The customer is required to report the amount of air that is exhausted. Also, they are interested in optimizing the combustion process by monitoring the amount of air flow during operation. The flowmeter’s bidirectional measurement meets this dual requirement:
“An essential advantage of t-mass 500 is its bidirectional measurement — the device has fulfilled our expectations," the customer stated.
CO2 measurements in a brewery
T-mass 300 is installed in a CO2 filling process where pressure release occurs. T-mass 300 is used for measuring both the filling as well as the reverse flow, resulting from pressure relief. The customer stated: “For us, it is good to have found a measuring device through which both the forward and reverse flow can be measured — due to the fact that we have a filling and pressure relief occurring through the same gas shuttle pipe of a beer tank. Using the data from this measurement, we are able to have a direct influence on the reduction of CO2 consumption, thereby lowering sustainably our CO2 footprint.”
HONORABLE MENTION: Sho-Rate 1250/55
Brooks Instrument
Glass tube variable area flow meter improves heat-treating application
To meet this need, the company chose to equip their furnaces with Sho-Rate Series 1250/55 glass tube variable flow meters from Brooks Instrument. The cost-effective Sho-Rate glass tube flow meters are ideal for many industrial uses, including panel display applications for liquids and gases, and feature an EZ-CHANGE tube design, along with options for aluminum or stainless steel fittings.
In this case, the Sho-Rate series provided several key features that made it a valuable measurement tool for the OEM’s products:
It provides tight flow control with up to 3% accuracy and 0.25% repeatability depending on the model — a key factor the furnace company highlights when promoting its products.
The Sho-Rate series features a rotating lens that provides a 180-degree view with magnification, making it easier for plant personnel to clearly view several meters at once or read the flow rate on the meter from any direction.
The EZ-CHANGE design allows quick interchangeability of tube assemblies to accommodate different flow ranges using a standard Allen wrench.
One-piece tube assemblies allow OEMs to stock assemblies with different flow rates to allow ultimate project flexibility, shortest lead times, cost reduction and serviceability.
Based on these features, as well as the proven reliability, accuracy and durability of Brooks Instruments products, the company chose to standardize on the Sho-Rate 1250/55 for measuring and controlling cooling gas flow on its furnaces.