When to specify metallic versus ceramic pressure sensors
In nearly every industry, pressure instruments provide essential condition monitoring to help processors optimize control, safety and efficiency. These devices translate pressure changes into electrical signals for consumption by host control systems, triggering both automated and manual operational adjustments to hold process conditions at ideal points. From monitoring hydraulic systems in manufacturing facilities to regulating pressure in various pipelines, these instruments are imperative for ensuring smooth operations and preventing costly malfunctions.
Specifying the right types of pressure sensors in every operation is an essential component for success. The membrane material plays a critical performance role, impacting suitability in different applications. A membrane contacts the process media under measurement, deforming slightly under pressure. This deformation within the sensor creates an electrical signal, which is sent to a host — such as a control or an asset management system — by a transmitter. Therefore, the choice of membrane material can significantly influence a sensor's performance, lifespan and suitability for a process (Figure 1).
Metallic and ceramic membranes are two of the most common choices, each with advantages and challenges depending on the operating environment and process requirements. Understanding these distinctions is critical for selecting the right material in every application, and this article outlines each of the strengths and challenges of each type.
Metallic and ceramic membrane comparison
Properly specifying metallic versus ceramic membranes for use in an application requires a thorough understanding of their material properties, performance characteristics and suitability in different process media (Table 1).
These considerations are detailed throughout the sections that follow.
Material properties and construction
Metallic membranes are typically constructed from stainless-steel alloys — such as SS-316L, which is the most common — chosen for their balance of flexibility, strength, cost-effectiveness and relative resistance to corrosion. The manufacturing process usually entails cold working and welding to shape the membrane and integrate it into a sensor housing.
While stainless steel provides reasonable fatigue resistance, it is susceptible to corrosion in particularly harsh environments, including acidic or alkaline process media, as well as those containing chloride ions. These limitations necessitate diaphragm seals or other barriers to process media intrusion in these types of environments, adding complexity, increased error and potential points of failure.
Furthermore, metallic membranes are sensitive to extreme temperatures, with fluctuations causing measurement drift that can adversely impact accuracy. Alleviating this condition requires measurement compensation or temperature control. Different alloys, such as nickel- and copper-based, can be used for enhanced corrosion resistance, but these specialized materials typically cost more than stainless steel.
Conversely, ceramic membranes — especially those made of Ceraphire, which is 99.9% pure aluminum oxide — provide superior hardness, chemical inertness and temperature stability compared to their metallic counterparts. Ceraphire membranes are even capable of withstanding absolute vacuum conditions, without the need for any fill oil.
Ceraphire is manufactured through a sintering process that results in a dense, non-porous material with extremely robust physical properties, giving it high resistance to abrasion, corrosion and hydrogen diffusion. Furthermore, its low porosity eliminates the need for additional protective coatings or seals in most applications, simplifying sensor design and alleviating potential leak points.
Ceramic materials’ high temperature stability minimizes sensor drift and ensures accurate readings over a wider temperature range than metallic diaphragms. The thermal expansion coefficient of Ceraphire is also well-matched with common sensor housing materials, such as aluminum and brass, reducing thermally induced stresses. Additionally, Ceraphire membranes do not sustain damage from typical blunt object impact, or during routine calibration and maintenance.
Performance characteristics
Metallic membranes perform well in controlled environments, although their dynamic response in most designs is affected by membrane thickness and the properties of fill oil used in the sensor. In the presence of harsh process conditions, sensors with metallic membranes can drift over time due to material fatigue, leakage and other environmental factors.
These types of membranes are also sensitive to overpressure spikes, which can cause permanent deformation, or even rupture a diaphragm seal. For these and other reasons, it is best practice to accompany metallic membrane sensors with overpressure protection devices.
Ceramic membranes provide higher long-term accuracy, better stability and improved resistance to overpressure and drift compared to metallic options. Their material stiffness contributes to excellent linearity and repeatability in pressure measurements, and their broader operating temperature range and lower sensitivity expand applicability, reducing the need for complex temperature compensation considerations. Additionally, the high natural frequency of ceramic membranes yields faster response times, providing faster measurement updates.
Applications and suitability
Metallic membrane pressure sensors are commonly used in general-purpose applications where cost is a key driver and environmental conditions are relatively benign, such as HVAC systems, pneumatic controls and some hydraulic applications. They are well-suited for less demanding environments, temporary installations and pilot projects, where pinpoint accuracy and long-term stability are not of paramount concern. The higher flexibility of metallic diaphragms compared to ceramic alternatives also renders them optimal for use in low-pressure applications.
On the other hand, ceramic membranes excel in extreme environments, including harsh chemicals, abrasive materials, high temperatures and hydrogen-rich settings. They are the preferred choice when reliability, longevity and high accuracy take precedence over cost constraints. They are frequently used in chemical processing, oil and gas and wastewater treatment applications.
The robust nature of ceramic membranes often eliminates the need for diaphragm seals, simplifying sensor specification and installation, while high overload resistance also makes them ideal in applications with potential pressure spikes. Because ceramic membranes are more robust than their metallic counterparts, calibration can be performed at a lower frequency.
Case study: Industrial water treatment and separation
A large industrial facility treating raw river water for use in its manufacturing processes was experiencing persistent reliability issues with metallic membrane pressure sensors. These sensors, critical for monitoring various treatment stages, were frequently damaged by small debris and abrasive contaminants present in the raw water, which caused inaccurate readings, clogging and even outright sensor failures. The facility experienced an average failure rate of one sensor every month, each resulting in hours of downtime and significant production losses.
To address these challenges, the company piloted Endress+Hauser Cerabar PMC71B pressure instruments with ceramic membranes, installing them in the same challenging locations alongside its older metallic membrane sensors. The robust ceramic membranes were uninhibited by the abrasive particles, and after a year, the pilot program demonstrated a dramatic improvement compared to the base operation. No failures were recorded among the ceramic sensors, while metallic sensors in the control group continued to fail.
Switching over to the new ceramic membrane sensors significantly reduced downtime, calibration requirements and ongoing maintenance, while their increased accuracy also optimized chemical usage and enhanced process control. While the ceramic sensors cost more to initially install than the older metallic sensors, this difference was quickly offset by reduced annual maintenance and repair costs. Following the pilot’s success, the facility replaced all its metallic membrane sensors with ceramic versions, achieving long-term cost savings and improved operational reliability in its manufacturing processes.
Case study: Wastewater treatment
A municipal wastewater treatment plant was experiencing frequent failures of metallic membrane pressure sensors in its anaerobic digesters. These sensors, required for monitoring both level and pressure, frequently succumbed to harsh environmental conditions, which contained corrosive hydrogen sulfide, aggressive chemicals and abrasive solids.
To maintain operations, the plant was replacing these sensors every three to six months, incurring significant ongoing expenses and process disruptions. Frequent failures also compromised measurement reliability, hindering optimal digester performance and biogas production.
Seeking a durable solution, the municipality installed Endress+Hauser Cerabar PMC71B pressure instruments with ceramic membranes, well-suited to harsh environments. Following installation, the plant observed a marked improvement, including dramatically longer sensor lifespan of over two years on average, an increase by a factor of four to eight. These improvements reduced downtime, maintenance and labor costs, while optimizing operational efficiency by providing accurate data continuously.
Make informed decisions
The right choice for specifying metallic versus ceramic pressure membranes comes down to application requirements. Metallic membranes are typically more cost-effective in less demanding settings where corrosion and abrasion are not major concerns, while ceramic membranes excel in harsh environments, including those with corrosive chemicals, abrasive materials and high temperatures.
Ceramic membranes usually require higher upfront investment, but they provide higher accuracy, stability and longevity over metallic alternatives, reducing maintenance costs and downtime. When specifying pressure sensors, processors must take operating conditions and performance requirements into account to make the best choice.
There are numerous factors to consider, so consulting with leading suppliers is highly recommended. With expert guidance based on the unique challenges and demands of every application, processors can ensure the best instrument technology selection for optimal ongoing production.
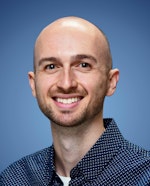
Nick Hanson | Water & Wastewater Industry Marketing Manager for Endress+Hauser USA
Nick Hanson is the Water & Wastewater Industry Marketing Manager for Endress+Hauser USA. In this role, he is responsible for strategic market planning and industry outreach events. As part of the Endress+Hauser Global Strategic Industry Group, he acts as the voice of the U.S. market to guide solutions specific to the region. Nick has a Bachelor of Science degree in Mechanical Engineering from the University of Colorado Boulder, and he has worked in the process instrumentation and control industry since 2011.