Solving traditional temperature measurement challenges
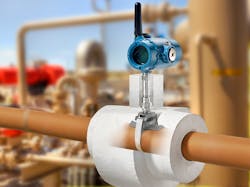
Temperature is often one of the most measured variables in a typical processing plant. Obtaining temperature measurements at various points along the process flow is an important part of monitoring or controlling a process.
But measuring inside the pipe presents challenges. Thermowells installed inside pipes are the most common solution used to measure process temperature. However, thermowells have significant design, engineering, installation and maintenance costs.
By comparison, one of the latest innovations in temperature measurement, Emerson’s Rosemount X-well Technology, measures process temperature without a thermowell, providing similar accuracy without requiring a process shutdown to install.
Below is a short overview showing the differences between thermowells and Emerson’s solution without a thermowell, along with some recent innovations and application best practices.
Thermowells
Thermowells are used in many different applications, such as pipelines, heat exchangers and wellheads. They act as a barrier between a process medium and the sensing element of a temperature-measuring device. Thermowells are carefully designed to fit specific pipes and process fluid conditions. To ensure that thermowells can withstand these conditions, an engineer will typically perform wake frequency calculations. They will also need to consider compatibility between the thermowell and process fluid to avoid corrosion. Abrasion from heavy particulates and high-velocity flow rates can also lead to thermowell failure.
Thermowells are used throughout a variety of different industries. However, they can be problematic for many reasons, including introducing potential leak points and undergoing complex and time-consuming design and installation. They are also impractical for small line sizes and will often require significant pipe modifications in these applications. Process shutdowns are required for installation. This drives up the total lifecycle cost and reduces throughput.
In the case of small line sizes, Rosemount X-well is an excellent solution, as it is non-intrusive, meaning it does not require pipe penetration. In side-by-side comparisons, this new technology has been shown to provide similar or sometimes even better performance since a thermowell’s stem conduction error is more significant in these small line size applications.
Traditional surface measurement
Surface temperature measurements made on the outside of the pipe eliminate many of the pains associated with thermowells as they do not require direct contact with the process. However, this approach cannot match the measurement performance of a thermowell installation.
If a true process temperature measurement is needed, a surface temperature measurement often cannot provide an accurate or repeatable representation of an internal measurement. Varying ambient temperatures can severely impact a surface measurement reading, leading to unpredictable output.
Attempts to relate surface temperature to process temperature can also be problematic. Even a consistently applied correction to the surface temperature measurement to equate it to an expected temperature drop through a pipe or vessel wall loses validity if either the process or ambient temperature changes. The surface sensor and associated mounting assembly can act as a “heat sink,” absorbing heat from either the process or external environment, producing inaccuracies similar to stem conduction errors common in small line-size thermowell installations.
Rosemount X-well Technology and measurement success
As mentioned earlier, this technology (shown in Figure 1) eliminates the need for a thermowell or process penetration without compromising reliable and accurate process temperature measurements. It uses measured ambient and pipe temperatures along with user-provided pipe characteristics to calculate the process temperature using a thermal conductivity algorithm created by Emerson, the first company to introduce non-intrusive process temperature measurement.
With no pipe intrusion, potential leak points are eliminated. Unlike traditional surface temperature measurements, this measurement technology relies on both surface and ambient temperature to determine the process temperature. This allows the device to account for heat loss from the pipe to the environment (Figure 2).
Designing a Rosemount X-well solution requires only three basic parameters: pipe diameter, pipe schedule and pipe material. These values determine the thermal conductivity and thickness of the pipe, which are both direct inputs into the device’s heat flux algorithm. This technology is available in both 4-20 mA wired HART and WirelessHART outputs. Wireless enables faster commissioning upon start-up and makes it easier to accommodate late-stage project changes.
This technology is most responsive in applications that include highly conductive pipe materials, thin pipe walls, liquid processes and high-velocity flows. Due to its reduced time response compared to thermowells in most conditions, this technology is not intended for use in safety loops, fast control or custody transfer applications. It is suitable for the vast majority of temperature monitoring applications. In addition, applications including small line sizes, high-velocity flows, heavy particulates, exotic materials and frequent cleaning greatly benefit from the technology.
Changes to pipe or vessel wall properties will impact the algorithm’s performance. The algorithm is based on a set collection of pipe property parameters, and if a change occurs, accuracy will be affected. Scaling or buildup inside the pipe will impede thermal conductivity through the pipe and negatively affect the accuracy of the temperature measurement calculation. External buildup on the pipe (at the sensor contact point) and thinning of the pipe material will similarly impede accuracy. If pipe thinning or scale buildup can be quantified, manual adjustments to the algorithm can be made to account for these factors. As a best practice, debris on the outside of the pipe should be removed. Operators should ensure that the temperature sensor is making good direct contact with the surface of the pipe to maintain measurement integrity.
Other performance considerations are proper fluid mixing and sensor placement. Fluid must flow sufficiently in a pipe to produce a uniform cross-sectional temperature. Without this, large temperature gradients may develop within the pipe. It is also important that the surface sensor is in contact with the part of the pipe that contacts the internal fluid. If the pipe is half full, the sensor must be placed on the lower half of the pipe.
Universal Pipe Mount offers an improved mounting solution
As explained earlier, Rosemount X-well is installed on the outside of the pipe, circumventing the many pitfalls of thermowells. Traditional pipe mount clamps can be heavy and cumbersome to install, especially on large line sizes. The latest upgrade uses a unique Universal Pipe Mount design that utilizes a cut-to-fit banding solution.
Vibration and pipe expansion or contraction, caused by changes in process temperature, can compromise the measurement integrity of static mounting solutions. The Universal Pipe Mount’s integral spring assembly, along with the spring-loaded RTD, allow for these fluctuations while still maintaining solid contact with the outside of the pipe. The result is a reliable and accurate process temperature measurement. This type of reliability gives operators confidence in their temperature monitoring applications.
The universal design allows operators to keep an inventory of units on hand for rapid deployment if emergency measurement needs ever arise. The only factor to consider in these cases is line size, which is addressed by simply using the appropriate length of non-proprietary banding, suitable up to 60-inch (DN1500) line sizes. This design also utilizes removable tension rods, allowing for quick uninstallation and/or reinstallation while preserving the banding loop’s form for use on the same or similar-sized line.
Improving outcomes
Rosemount X-well Technology makes it possible to obtain reliable temperature measurements from any point on the pipe, providing users with the data to optimize their process.
- To sum up the benefits of using Rosemount X-well Technology:
- Increased production as install and troubleshooting does not require shutdowns.
- Reliability and safety as it eliminates leak points.
- Reduced lifecycle costs since the technology requires less maintenance and minimal failure risk.
- Reduced design and installation costs. There is no need for complex calculations and design work.
- No need for specialized installation technicians and welders.
- Accommodate change; late design changes no longer require significant engineering efforts. The only information required is pipe diameter, material and schedule.
- Greater flexibility for the customer and engineering, procurement and construction (EPC) contractors when designing a new process.
Simplifying temperature measurement increases safety and reduces costs, especially when dealing with hazardous processes. Adding additional measurement points paints a more complete picture of the overall process, highlighting potential trouble spots that otherwise might be missed until they trigger a costly process shutdown.
This innovative solution allows for measuring process temperatures in a safer and more cost-effective manner.
Roger Morrison is a global product manager for Emerson in Shakopee, MN, responsible for Rosemount temperature transmitters and Rosemount X-well Technology. Morrison holds a BS in mechanical engineering and an MBA from the University of Minnesota.
Ryan Leino is a senior product manager for Emerson in Shakopee, MN, responsible for the Rosemount temperature transmitter and Rosemount X-well Technology portfolio. Leino holds a BS in chemical engineering from the University of Wisconsin and an MBA from the University of Minnesota.
Emerson
Roger Morrison | Global product manager for Emerson
Roger Morrison is a global product manager for Emerson in Shakopee, MN, responsible for Rosemount temperature transmitters and Rosemount X-well Technology. Morrison holds a BS in mechanical engineering and an MBA from the University of Minnesota.