It is useful to introduce the topic of steam by first considering its use in industry. Steam use is an essential part of most modern process facilities. Steam provides a convenient way of transporting energy throughout a facility. That energy is most commonly used for heat transfer, power generation, mechanical work, sterilization and humidification.
In recent years, there has been an increased focus on energy production and conservation. Environmental regulations and financial incentives are the primary drivers of this increased focus. As a result, more attention than ever is being paid to steam generation and use.
Types of steam
As heat is added to liquid water at constant pressure, its temperature increases until the boiling point is reached.
Further heating breaks the bonds between water molecules and changes liquid water into vapor (steam) at a constant saturation temperature. This mixture of liquid water and gaseous steam is referred to as “wet steam” or “saturated steam.” As more heat is added, the percentage of steam to liquid water increases. When the heating has converted all the liquid water to steam, further heating starts to raise the temperature of this superheated steam. (See Figure 2.)
Wet steam is the most common type of steam experienced by most process facilities. When a boiler produces steam, it usually contains some water droplets that were not vaporized and carried over into the steam piping.
What is steam quality?
Steam quality is a measure of the wetness of steam. Typically, steam quality is expressed as a percentage (X), where the mass of steam is divided by the sum of the mass of steam and water.
As more heat is added to the steam, the evaporation increases, causing the percentage of vapor to increase as the percentage of liquid decreases. This results in the steam quality (X) increasing until it reaches dry steam (X=100%). (See Figure 3.)
The importance of steam quality
Steam use is a vital part of most modern process facilities. As such, steam quality should be measured and controlled to acceptable standards. Unfortunately, steam quality is typically not monitored closely and is assumed to be 100%. Therefore, issues that arise from poor steam quality are often attributed to some other system component. This often leads to disastrous safety and economic consequences.
Safety considerations
Poor quality steam has a significant percentage of liquid water present. This liquid water can severely damage piping and process equipment, including erosion of critical components such as valves, pressure regulators and turbine blades. The presence of liquid water also leads to more corrosion due to the increased presence of carbonic acid.
Pressure surges of liquid water create severe impacts, also known as water hammer. In extreme cases, water hammer can damage piping components so severely that dangerously hot steam and water spew out into the surrounding environment.
Economic considerations
Steam quality is a reliable indication of the energy content of the steam. Higher quality steam contains more useable energy. More useable energy translates to greater efficiencies of the work being performed. This ultimately allows for reducing boiler load and the associated costs. Process operations can also benefit from higher-quality steam by increasing throughput. Direct steam heating applications benefit from higher-quality steam by reducing quality issues and preventing batch rejections.
How to measure steam quality
Historically, measuring steam quality was only feasible through the use of a throttling calorimeter. This device takes a steam sample through a throttling orifice into a well-insulated expansion chamber. Temperature and pressure measurements are taken, and through the use of steam table calculations, a steam quality value is determined.
There are some inherent drawbacks to this type of manual testing. Since the testing results depend heavily on the technician's skill, there is considerable potential for operator error. Also, because the testing is manual and not automatic, it is time-intensive and potentially unsafe, and it does not allow for trending the data over time.
Recent advancements have led to more innovative and practical methods of steam quality metering. Some vendors now offer sampling methods similar to the throttling calorimeter that are fully automated and capable of communicating with modern control systems. Other vendors have taken a different approach altogether and have gone away from the sampling method, opting instead for inline designs that are capable of automated and continuous steam quality metering.
Common steam flow metering issues
Steam is one of the most challenging fluids to measure. High pressures, high temperatures, varying degrees of steam quality and different types of steam all contribute to the high degree of difficulty. Since steam is often used as a heating medium, there are also seasonality issues associated with steam metering. Often, steam flows vary a large degree between colder and warmer seasons. If a steam meter is sized for the maximum flows in colder months, it may not capture the warmer months' low flow conditions.
If the steam being metered is of poor quality, there can be additional issues. Poor quality steam has liquid water present. Pressure surges of liquid water can damage flow metering equipment such as primary elements, turbine blades and velocity sensors.
The presence of this liquid water can also lead to the overreading of steam flow rates. Most single-phase steam flowmeters assume only one phase is present — the vapor phase. Therefore, they do not capture the water component of the steam and water mixture. This leads to the meter overreading steam flow rates.
Flowmeter technologies for steam metering
Vortex steam metering
Vortex flowmeters measure steam flows by detecting the frequency at which vortices are alternatively shed from a bluff body. (See Figure 5.) The frequency at which these vortices are shed is directly proportional to the flow velocity.
Adding temperature and pressure measurements in conjunction with a flow computer allows for the calculation of a compensated mass flow rate. Some vendors offer these upgrades in the form of a multivariable vortex flowmeter.
- Simple and robust construction; no moving parts.
- Multivariable models can provide a compensated mass flow measurement.
- Relatively low permanent pressure drop.
- Relatively high turndown ratio.
- Requires very little maintenance.
- Insertion-style meters are an economical option on large line sizes such as steam headers.
- Insertion-style meters can be installed under full process conditions.
- Key disadvantages of vortex steam metering include:
- Poor performance at low flow rates.
- Requires unobstructed upstream and downstream straight piping lengths.
- External vibrations can cause measurement errors.
Differential pressure steam metering
Differential pressure flowmeters measure steam flows through the use of Bernoulli's equation. A primary element creates a pressure drop across the flowmeter by introducing a constriction in the pipe. Impulse piping routes the upstream and downstream pressures of the flowmeter to a differential pressure transmitter. From there, Bernoulli's equation is used to calculate a volumetric flow rate.
Multivariable differential pressure flowmeters add temperature and static pressure sensors. With these additional sensors, a compensated mass flow measurement is possible.
Key advantages of differential pressure steam metering include:
- Simple and robust construction; no moving parts.
- Relatively inexpensive.
- Multivariable models can provide a compensated mass flow rate.
- Key disadvantages of differential pressure steam metering include:
- Relatively high permanent pressure drop. Dependent on the type of primary element used.
- Limited turndown ratio.
- Interference with the flow stream.
- Primary element will wear over time.
- Requires unobstructed upstream and downstream straight piping lengths. Dependent on the type of primary element used.
Turbine steam metering
Turbine flowmeters measure steam flows by detecting the rotational velocity of a turbine rotor in the flow stream. The rotational velocity of the turbine rotor is directly proportional to the fluid velocity flowing through the turbine. Blade movement is most commonly detected magnetically, with each blade generating a pulse to be measured by an electrical pickup.
Adding temperature and pressure measurements in conjunction with a flow computer allows for the calculation of a compensated mass flow rate. Some vendors offer these upgrades in the form of a multivariable turbine flowmeter.
Key advantages of turbine steam metering include:
- Excellent performance at low flow rates.
- Multivariable models can provide a compensated mass flow measurement.
- Relatively high turndown ratio.
- Relatively low permanent pressure drop.
- Insertion-style meters are an economical option on large line sizes such as steam headers.
- Insertion-style meters can be installed under full process conditions.
- Key disadvantages of turbine steam metering include:
- Condensate and boiler carryover can harm the turbine blades and interfere with measurement accuracy.
- Moving parts require regular maintenance.
- Requires unobstructed upstream and downstream straight piping lengths.
Conclusion
Steam use is and will continue to be an essential part of modern process facilities. Understanding the different types of steam is critical to understanding how to utilize the benefits of steam. The lesser-known steam quality measurement can significantly affect both safety and economic considerations in steam systems. Historically, measuring steam quality has been a challenging manual process. Recent advancements have led to more innovative, practical and automatic methods.
High pressures, high temperatures, varying degrees of steam quality and different steam types all contribute to the high degree of difficulty of steam flow metering. However, there are several suitable technologies for steam metering, with each technology having its own merits and limitations. The specific application should help determine which technology is most suitable.
Ryan Bennett is a product marketing manager for VorTek Instruments in Longmont, Colorado. He holds a B.S. in industrial distribution from the University of Alabama at Birmingham. Bennett has had a strong focus on steam metering, control and distribution throughout his career. He has worked in various roles at VorTek Instruments, with a current focus on new product development and marketing. Bennett can be reached at [email protected].
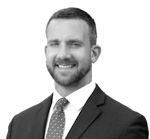
Ryan Bennett | Product marketing manager
Ryan Bennett is a product marketing manager for VorTek Instruments in Longmont, Colorado. He holds a B.S. in industrial distribution from the University of Alabama at Birmingham. Bennett has had a strong focus on steam metering, control and distribution throughout his career. He has worked in various roles at VorTek Instruments, with a current focus on new product development and marketing. Bennett can be reached at [email protected].