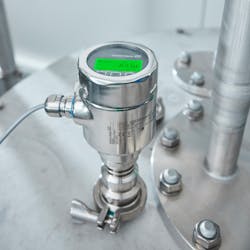
As the life sciences industry increasingly adopts continuous processes in place of batch processes, pharmaceutical processors are steadily elevating operational efficiency, while providing faster drug manufacturing lifecycles and increased production. This steady improvement is possible because of substantial automation advancements at various stages throughout processing, including instrumentation enhancements in measurement accuracy, increased diagnostic data, simplified maintenance and assured regulatory compliance.
Continuous processing is even more sensitive to downtime than batch processing, making diagnostic data and preemptive failure alerts in plants more imperative than ever in these types of environments. Additionally, the FDA states in Section B.6 of its Quality Considerations for Continuous Manufacturing Guidance for Industry (Equipment Control Strategy):
Throughout the product life cycle, the development and maintenance of the control strategy should take into account equipment failure modes to ensure that abnormal equipment performance is detected and investigated, including appropriate corrective action. Equipment maintenance and calibration procedures should be developed and updated based on ongoing monitoring of equipment performance and other available information… This can also help to determine the maximum run time for the integrated line before maintenance or cleaning is needed.
This article will focus on recent advancements in radar level measurement, which are empowering life sciences users to measure with accuracy, increase process uptime, extend calibration intervals and maintain regulatory compliance.
Classical radar challenges: a tall order
There are numerous ways to determine level in process applications, and each technology has strengths and weaknesses, pros and cons. Radar level measurement is among the easier to implement in many situations because measurement is non-invasive and does not require contact with the actual process media. However, applications and conditions for deploying radar level technology historically were relatively limited.
Conventional radar instruments operate at low frequencies, requiring wide beam angles to measure process media height. These wide beams are especially sensitive to obstacles within a tank, as well as being susceptible to interference from tank walls.
Additionally, foaming within the vessel media or buildup accumulation on the radar antenna can interfere with the reflected signal, creating measurement inaccuracies that disrupt process control systems. These sorts of issues can be mitigated with frequent preventive maintenance, but that requires shutting down processes, removing the instrument from service for cleaning, reinstalling the instrument and restarting the process, risking process contamination and wiring errors upon instrument replacement.
Particularly in pharmaceutical clean-in-place and steam-in-place processes, instrumentation must be easy to clean, resistant to disinfectants and other chemicals, hygienic — for example, in a watertight 316L stainless steel housing to avoid contamination — and able to withstand extreme temperatures. These requirements further limit level instrumentation selection, adding to the challenges posed by tank geometry and process media characteristics.
And finally, in accordance with FDA 21 CFR sec. 820.72 and DIN EN ISO 9001:2015 sec. 7.1.5/7.1.5.2a, processors must ensure instrumentation is suitable for its intended purpose — and it is calibrated, inspected, checked and maintained regularly — with supporting documentation. Continual calibration and maintenance-imposed removal from service, along with proper documentation of these activities, creates challenges and introduces further downtime.
Fortunately, smart 80 GHz sensors provide solutions to these and other issues.
Beam-focused solutions
80 GHz radar level sensors are gaining traction in multiple industries due to their technological advancements over earlier generations of radar level instruments, significantly increasing application flexibility.
Most importantly, 80 GHz transmitters use a narrow, focused signal beam, making it easier to avoid interference from tank walls and obstacles, install them in exterior nozzles without using antenna extensions and even shoot the beam through ball valve attachments (Figure 1).
With fewer sources of interference — which cause signal energy loss — to contend with, these instruments can measure at greater distances, and in media with lower dielectric constant values. Combined with false echo suppression and improved dynamic range of up to +20 decibels over predecessors, the narrow beam also increases the possibilities for measuring level in tanks and silos with complex geometries. In addition, modern microprocessor chips provide faster signal processing for detailed diagnostics and timely measurements, and this information can be transmitted to central process control and monitoring systems.
Advanced instrument diagnostics enable predictive maintenance, such as identifying possible leakage currents due to water in housing, wiring issues or corroded terminals in a junction box. This is done by continuously monitoring loop voltage and current without process interruption, giving early warning of these sorts of issues, each of which can cause critical device failures if left unaddressed.
Diagnostic data can also be used to automate process adjustments, like changing antifoam agent dosing when foam is detected by micro-interferences in the radar signal (Figure 2).
Another example is automating an air purge when build-up is discovered in applications using an antenna.
Digital communications ease configuration and maintenance
Digital communication protocols provide transmission of instrument diagnostic and additional process data. Ready for the Industrial Internet of Things (IIoT), modern smart instruments can be configured to generate alerts when detecting certain conditions, such as low storage tank levels, so additives or ingredients can be replenished before they run out.
These protocols also support remote configuration, maintenance and verification — in some cases, wirelessly. For example, Endress+Hauser’s smart instruments empower plant personnel to connect to instruments from upwards of 30 feet away using a Bluetooth app running on a smartphone or tablet (Figure 3).
When performing maintenance, this eliminates the need to open electrical panels, remove protective housing covers and scramble through tight or dangerous spaces to access hard-to-reach devices. It also alleviates the need to keep dedicated wired plant communicator devices’ batteries charged, device type manager catalogs current and firmware updated.
The Ethernet-APL physical transport layer is a recent instrumentation development that provides the ability to transmit digital data via industrial Ethernet protocols using a single two-wired shielded cable per instrument. Ethernet-APL supports multiple industrial protocols — including but not limited to PROFINET, EtherNet/IP, Modbus TCP, HART-IP and OPC UA — while providing high-speed data transmission at 10Mbit/s, making it possible to send and receive more data than is possible with older digital methods.
Ethernet-APL instruments possess embedded web servers, making configuration accessible from any device capable of running a web browser — such as a laptop, smartphone or tablet — via the instrument’s IP address, without any need for specialized instrument communicators. These browser-based interfaces typically include parameterization, report creation and troubleshooting tools, along with guided configuration workflows, event logbooks and firmware update mechanisms.
Using Bluetooth, Ethernet-APL or traditional HART interfaces, users can configure instrumentation quickly and accurately with guided wizards. These wizards reduce “menu-hopping,” substantially shortening commissioning time, while mitigating errors, such as incorrect entries and forgotten parameters. SIL commissioning and proof-test wizards are also often available, ensuring instrument verification procedures are conducted in accordance with applicable standards.
Level measurement with reliable foam detection
One biopharmaceutical processor needed a level measurement solution simultaneously to measure level and detect heavy foam buildup in a live culture tank. To achieve this, it installed Endress+Hauser’s Micropilot FMR63B 80 GHz radar level instrument for hygienic applications, providing foam detection and a host of additional data to ensure maximum process uptime.
Designed to ASME BPE, 3-A, EHEDG, and other hygienic industry standards, the FMR63B instrument provided continuous transmittance of diagnostic data, and it extended the required time between calibration cycles using Endress+Hauser’s traceable Heartbeat Technology performing verification. This verification is performed in-situ, increasing process reliability and uptime, and the instrument is IEC61508-compliant, with a CRC checksum to minimize operation errors.
The processor benefited from Heartbeat Verification Radar Accuracy Index (RAI), a patented technology that assesses sensor reference accuracy without process interruption. Certified ISO9001-compliant, and traceable to national standards, this deviation parameter was used to extend calibration intervals, while simultaneously verifying radar measurement accuracy between wet calibrations.
Accessible from either the SmartBlue app or the embedded Ethernet-APL web server, the processor also configured regular, automated verification reports. These reports include verification pass/fail results for the mainboard module, sensor module, RAI and loop diagnostics. Monitoring information is also provided, such as foam index, build-up index and minimum and maximum process values.
Equipped with reliable foam monitoring, the processor optimized the foam retardant dosing to continuously meet process needs. This reduced operational costs by alleviating foam retardant overdosing as well as the additional cleaning required to remove excess substance from the final product.
OT and IT advancements merge
Digital protocols and smart instrumentation provide indispensable data, which can be used to create operational and maintenance insights. Paired with sensor technology advancements, processors in the life sciences industries have significantly greater instrumentation options for monitoring and optimizing their processes.
Equipped with digital interfaces at their fingertips to manage both operations and maintenance, these enhancements are driving the shift to continuous processing by increasing measurement accuracy, process safety and facility uptime.
Bethany Silva is the Life Science Industry Manager for Endress+Hauser, a global process and laboratory instrumentation and automation supplier. In this role, she is responsible for the strategic direction, vision and growth of the Life Science unit in the U.S. Silva earned a certificate in bioprocessing for engineers from the Worcester Polytechnic Institute, and she has over 20 years of process industry experience, holding positions in R&D, process development, marketing and technical sales.
Keith Riley is the National Product Manager for Level and Pressure at Endress+Hauser. He has been with the company since April 2008. Prior to this, he was a Product Manager and Regional Sales Manager with L.J. Star Incorporated, as well as a Product Manager for Penberthy (Tyco Valves). Overall, he has over 20 years of sales, marketing and instrumentation experience in the process industries.
Endress+Hauser