Get expert operating analysis with remote valve condition monitoring
It is no secret that automated valves are critical to most processes. Their unanticipated failure can cost millions of dollars in lost production every year, so every facility has a strong incentive to keep their valves operating as expected. One of the best ways to do this is by detecting performance degradation before it transitions to functional failure.
Opportunity present but rarely utilized
Fortunately, many users have already installed digital positioners with advanced sensors and diagnostics on their valves to detect potential problems — well in advance of outright failure. Unfortunately, only a small fraction of plants utilize this capability to its full extent, and many plants barely use diagnostic capabilities at all.
The reasons are many. Some positioner diagnostics are only run when the valve is offline, greatly limiting the opportunity to do any testing. Other plants have positioners with online diagnostic capability, but simply lack the time and resources to take advantage of the available data. In fact, many users end up reviewing positioner diagnostic features only after the valve has failed. Use of diagnostics after failure is helpful for troubleshooting, but it could have been more effectively used to predict and possibly prevent failure.
Remote valve monitoring closes the gap
Remote valve monitoring provided as a service by third-party experts delivers continuous monitoring of critical automated valves, without exerting a drain on limited plant resources. This type of valve condition monitoring takes advantage of the digital positioner diagnostics already installed in many plants. These digital controllers sense valve travel, drive signal, temperature, cycle count, travel deviation, supply air pressure, friction/torque, valve stroke time and other parameters.
Based on instantaneous and trended data, it is possible to detect most developing problems before the valve fails (Figure 1). However, this data is only useful if it is gathered in near-real time and is accessible by an individual with the tools, skills and time to interpret it.
Emerson provides these services by first utilizing its Fisher ValveLink software to perform scheduled online testing of each valve as it operates. Data is automatically gathered if the positioner detects an abnormal condition. All of this information is securely transferred to Emerson for review.
Data security is paramount to virtually every company, and Emerson provides its services with cybersecurity built in. Data can be transferred in a variety of methods, each discussed and approved by the end user’s IT staff. Data files can be emailed on a weekly basis, automatically transferred via a wireless network and a data diode (Figure 2) or transferred via a secure data highway and firewall set up by the users’ IT department.
Once the data is delivered, Emerson experts, serving as an extension of on-site staff, review and analyze the diagnostics information via a cloud-based analytics platform. The analysts, who are factory trained and certified, look at the current data and monitor historical data trends to identify performance degradation or developing mechanical problems. These services are delivered through a combination of manual monitoring and automated functions.
Some of the issues typically found include:
- Air supply or filter regulator problems.
- Actuator or diaphragm leaks or damage.
- Valve packing issues (too tight, too loose, leaking packing).
- Valve oscillation, limit cycling or tuning concerns.
- Valve inability to reach or maintain set point (travel deviation).
- Positioner overheating.
- Poor valve performance near end points, such as lack of shutoff or a failure to fully open.
- Insufficient stroke time.
Non-critical issues are noted in a monthly report (Figure 3) that documents the overall health of each valve and notes the problems’ impacts and recommended corrective actions. Developing issues are flagged well in advance so the plant can plan for repairs.
If critical problems are detected, the end user is notified immediately so they can address the issue. In most cases, performance declines are detected weeks in advance of failure, so plant personnel have sufficient time to plan and execute the repair. This allows for the transition from reactive maintenance to predictive maintenance, improving plant uptime and profitability, while reducing repair costs, and improving safety by avoiding incidents.
Any plant with critical automated valves and a limited staff is a good candidate for this type of service, but remote valve condition monitoring is particularly advantageous in certain applications, as detailed in the following examples.
Real-world savings
Pressure swing adsorption (PSA) units are common in many refining units and are often a critical part of the production train. PSA units incorporate a number of valves operating in high-temperature, high-cycle service. Despite the severe conditions, the valves must ensure virtually zero leakage and fast stroke times to achieve optimal service. Remote monitoring allows each valve’s performance to be constantly evaluated, with developing issues flagged early enough to avoid unplanned outages. This improved uptime translates directly into increased refinery production.
Another leading application for remote valve monitoring is heat recovery steam generator (HRSG) production units. These units employ a number of critical steam bypass valves that must have extremely tight shutoff during normal operation — while handling very high flow rates, temperatures and pressure drops during bypass modes. While operating in this manner, the valves must provide precise response, despite punishing conditions. Many HRSG units have a small operating staff, so having an outside service monitoring the key bypass valves and detecting problems can directly improve overall steam production and uptime.
A less obvious benefit of valve condition monitoring is the data it provides for future use in turnaround planning. Near real-time valve performance information can be used to make data-driven decisions when planning maintenance outages. By focusing on valves that have known problems, plants can save significant sums of money on parts and labor, while shaving significant time off turnaround schedules.
For example, a combined cycle power plant was overhauling every critical valve during each outage to maximize uptime upon restart. After installing upgraded digital valve positioners and implementing diagnostic alert software, plant personnel were able to focus their repair efforts more efficiently, saving $68,000 in one shutdown alone. Other plants have achieved average savings of $1,200 per valve by focusing repair efforts on valves that display performance problems and leaving the rest of valves as-is.
Conclusion
Predicting the future is no simple feat, but the advanced diagnostics found in smart, digital positioners can go a long way toward helping maintenance staff do exactly that. In many cases, plants may already have the required components and networks in place, and they only need to gather the data from these devices and make it accessible for monitoring and review.
When the plant lacks the resources to implement internal monitoring, that work can be outsourced to experienced, knowledgeable third-party experts focused on detecting problems before they become major issues. Programs to leverage advanced valve diagnostics and remote monitoring typically yield significant positive impacts on plant uptime and reliability, while cutting maintenance costs. Due to these types of results, Emerson surveys show a 20% annual increase in end user engagements for these types of services.
If your plant is suffering from unexpected shutdowns and high maintenance costs during outages, an investigation into the power of valve positioner diagnostics and remote valve condition monitoring may significantly improve your bottom line.
John Carlow has spent the last 17 years working for Emerson’s Lifecycle Services business, providing equipment repair, turnaround support and field services. Over that time, he has held a variety of management roles, and he is currently a business development manager.
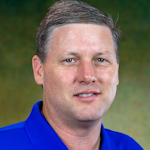
John Carlow | Business Development Manager, Emerson’s Lifecycle Services
John Carlow has spent the last 17 years working for Emerson’s Lifecycle Services business, providing equipment repair, turnaround support and field services. Over that time, he has held a variety of management roles, and he is currently a business development manager.