Control valves may have a direct and significant impact on plant efficiency, product quality, and safety. Valve performance is, therefore, a key focus as plant personnel face global competition and growing pressure to increase profits, boost plant performance, and improve process reliability.
These business realities have made valve diagnostics more important than ever. To keep a plant’s control valves performing optimally, plant personnel must be able to monitor valve performance and gather actionable information to use in diagnosing valve problems and planning maintenance activities. And they need to have this information in hand before valve problems impact process performance.
Presented here are two case studies that illustrate how valve diagnostics can help operations personnel make important maintenance decisions that can potentially improve process integrity, reduce maintenance costs, and increase output.
Case Study 1: Mapping Out Maintenance Strategies with Offline Diagnostics
A North American power plant was having difficulty controlling its turbine. The 20-inchFigure 1. The dotted lines in this graph show the expected signature for the steam conditioning valve described in Case Study 1, and the blue lines are the actual signature recorded. Friction was twice expected levels, preventing the valve from moving smoothly. The valve’s seating profile also was abnormal, with the “opening” line showing a shallow angle rather than a sharp transition from the closed position.power on the grid, resulting in approximately $1 million in lost production each day.
Removing such a large valve requires a crane and careful logistical planning. Offline valve diagnostics helped plant personnel determine whether this step was necessary.
The signature (Figure 1) clearly showed abnormally high and constant friction throughout the full stroke of the valve. Further, the seating profile depicted a non-sharp transition as the plug was moving in and out of the seat. (The dotted lines in Figure 1 indicate what would have been a normal level of friction and good seating profile.) These diagnostics indicated that there was a serious issue with the internal parts of the control valve.
Because of this information, the crew removed and disassembled the valve and found that surfaces of the plug and cage had been damaged by metal debris that had flown through the valve (Figures 3 & 4). The debris had become lodged in the holes of the cage, preventing the plug from sliding easily within the cage. In addition, the seat was damaged because the plug would slam into the seat, rather than smoothly touching it, because the excessive friction caused the plug to stick and then release suddenly.
The valve cage, plug and seat were repaired, and the valve was put back together. The plant was able to restart and the control valve controlled the flow of steam to the turbine, as expected. Offline diagnostic tools provided a valve signature that helped plant personnel make important maintenance decisions and then allowed the team to document the control valve’s performance after it had been returned to service.
Case Study 2: Online Diagnostics Provides Advance Notice of Pending Problems
By outward appearances, all seemed well with a process at a chemical plant producing PTA for the plastics industry. Operations personnel reported no problems with the process or the six-inch control valve controlling it. Online valve diagnostics (OVD), however, told a different story – the valve was showing signs of fatigue.
The control valve was adequately controlling the process, but the actuator required more thrust than typical to move the valve back and forth. The OVD technology detected that hysteresis had quadrupled in one month and found that positioning accuracy was poor (Figure 5). It was only a matter of time before process integrity and the quality of the product being produced would be impacted.
The valve was flagged to be repaired during an upcoming minor outage. At that time, the actuator was taken apart and technicians found that a degraded o-ring on the piston had created residue that prevented the piston from sliding smoothly within the piston chamber. The o-ring was replaced and the valve returned to service. Operators immediately reported having more robust control – not only of the process that the valve was controlling, but also of another process that was a slave of that loop.
Control valves are essential to a plant’s overall performance. By tapping the information today’s diagnostic tools can provide, operations personnel can help ensure their valves perform optimally and take a significant step in maximizing plant performance.
For more information about valve ?diagnostics and digital valve positioners, see “Evolution of Valve Diagnostics: Delivering Enhanced Process Control Under Increased Scrutiny” (Flow Control, August 2011) and “Mission Possible: Analog-to-Digital Valve Upgrades” (Flow Control, June 2011). You can find these articles under the Issue Articles tab.
Sandro Esposito is global marketing manager at GE Energy for digital and SMART products in the company’s Masoneilan product line. A 17-year veteran of the control valve and process automation industries, Mr. Esposito has extensive experience with control valve diagnostics and system integration and has been granted several patents related to digital valve positioners. He graduated from Ahuntsic College in Montreal with a degree in Instrumentation and Process Controls. Mr. Esposito can be reached at [email protected] or 281 671-1683.
www.ge-energy.com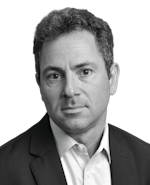
Sandro Esposito | Vice President of Sales & Marketing for SignalFire Telemetry Inc.
Sandro Esposito serves as Vice President of Sales & Marketing for SignalFire Telemetry Inc, with responsibilities for managing the portfolio and commercialization of the company’s wireless telemetry solutions. In addition to possessing more than 24 years of experience in the process control and automation industry, he holds six patents and has published 12 papers related to industrial controls and smart technologies. A graduate of College Ahuntsic in Montreal, he holds a Bachelors degree in electrical and instrumentation engineering and is actively involved in the International Society of Automation.