Going with (and accurately measuring) the flow
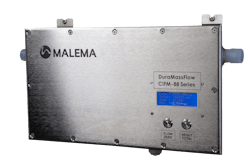
Our modern way of life, punctuated by everyday conveniences such as taking a shower or fueling a car, is underpinned by a silent army of technologies often taken for granted. Without these innovations, simple tasks and essential functions would revert to cumbersome and inefficient methods. Fortunately, a sophisticated infrastructure of pumps, pipes and processing equipment diligently transports vital fluids — water, chemicals and fuels — across the globe.
Within this network of technological marvels lies a crucial component ensuring the safe and accurate movement of these fluids: flowmeters. These devices are specifically designed to quantify the flow rate of fluids — whether liquids, gases or vapors — as they traverse pipelines, providing operators with essential, real-time data.
However, while flowmeters perform this indispensable function, traditional technologies often present limitations. Some flowmeters struggle to maintain accuracy when faced with fluctuations in a fluid’s handling characteristics, such as temperature, density and viscosity. These variations can lead to unreliable flow measurements, potentially compromising the integrity of the entire fluid-handling operation. Furthermore, the necessity for frequent calibration in other flowmeter designs can result in significant and costly periods of operational downtime.
Addressing these inherent challenges is the Coriolis flowmeter. This advanced technology delivers all the fundamental benefits of flow measurement while effectively mitigating the limitations of conventional designs. Its unique design and operational principle enable it to accurately measure a diverse range of fluids across numerous applications without compromising performance or requiring frequent recalibration.
This article will delve into the intricacies of Coriolis flowmeter technology, offering a comprehensive understanding of its functionality and an explanation of why it is exceptionally well-suited for demanding process and manufacturing environments within industries such as chemical, pharmaceutical, semiconductor and oil and gas, among others.
How Coriolis flowmeters work
The name of the Coriolis flowmeter originates from French engineer and mathematician Gaspard-Gustave de Coriolis, who discovered the concept of Coriolis force, the effect of motion on a rotating body. An example is the Coriolis effect, which states that any moving body on or above the Earth’s surface, such as an ocean or air current, will tend to drift sideways from its course because of the Earth’s rotation. This discovery played a key role in oceanography, meteorology and ballistics, and was later used as a primary element in measuring a substance’s mass flow rate.
The Coriolis flowmeter directly measures mass flow rate by harnessing the principles of physics within its intricate design. Typically, a magnetic exciter induces oscillations in one or more flow tubes. In the absence of flow, these tubes vibrate uniformly, with the inlet and outlet oscillating in perfect synchronization (in phase). However, as fluid begins to flow, the Coriolis force comes into play. This force acts on the fluid, causing it to accelerate as it moves toward the point of maximum vibration and decelerate as it moves away, resulting in a subtle twisting of the flow tube(s). Highly sensitive sensors strategically positioned at the inlet and outlet precisely track this minute motion and quantify the phase difference between the oscillations at these two points. Crucially, the magnitude of this phase shift exhibits a direct and linear relationship with the mass flow rate of the fluid; a greater phase difference unequivocally signifies a higher mass flow rate. This elegant measurement directly yields the mass flow rate, a fundamental parameter in many industrial processes.
Other Coriolis flowmeters follow a similar configuration. Fluid flows into the sensor, consisting of two flow-sensitive elements that are vibrated relative to one another, like the tines of a tuning fork. Fluid interacts with the sensor dynamically in such a way that the sensor’s response is immune to the fluid’s chemical and physical properties, flow regime or variations in the flow-velocity profile. Fluid mass flow rate is determined by measuring the relative motion and frequency of the flow-sensitive elements.
Real-world examples
While Coriolis flowmeters use the same operational principle to achieve results, not all are constructed the same way. Malema, part of PSG, a Dover company, fabricates its patented CPFM-8800 Series Coriolis Flowmeters from Perfluoroalkoxy (PFA) polymeric material.
Semiconductor manufacturing applications, among many others, require all PFA-wetted surfaces for proper functionality, accuracy and chemical compatibility. The CPFM-8800 Series Coriolis Flowmeters are comprised of two assemblies: one containing the sensor and the other supporting electronics. The combination provides highly accurate measurements ±1%) of mass flow rate, total mass, and temperature.
The CPFM-8800 Flowmeter family features a measurement range of 50 g/min to 4,000 g/min, a fluid temperature range of 64.4°F to 122°F (18°C to 50°C) and a maximum operating pressure of 80 psig (5.5 bar). It is ideal for highly corrosive chemicals, ultra-high-purity chemicals, water, slurries or solutions with solids or entrapped gases, and fluids with varying density or viscosity.
The Coriolis principle does not only apply to flowmeters. Malema also manufactures Coriolis mass flow controllers in the CMFC-5000 Series and CMFC-6000 Series, a line of closed-loop flow controllers designed for high-purity fluids, such as deionized (DI) water, harsh chemicals and CMP polishing slurries used in the semiconductor industry.
CMFC-5000 and CMFC-6000 Coriolis Flow Controllers pair a Coriolis flowmeter with a high-purity control valve. In operation, the user inputs a set point through an analog signal. The flow control module’s electronics continuously compare this set-point value with the flow rate reported by the flowmeter and provide a constant feedback signal to modulate the control valve to maintain the desired set point. The control algorithm with the flowmeter and valve achieves fast, accurate and repeatable control.
The CMFC-5000 features a flow range from 50 g/min to as high as 5,000 g/min, while the CMFC-6000 has a flow range of 20 g/min to 4,000 g/min. Both flow controllers control the flow rate within ±1.5% of the set point, making them ideal for fluid-blending and fluid-dispensing applications. The controllers also feature a two-second response time with the ability to drop to under a second for most applications, two types of control valves and PTFE/PFA-wetted-part construction.
Malema has recently introduced a Coriolis flowmeter specifically designed for industrial applications. The CIFM- 88 Series DuraMassFlow PFA Coriolis Mass Flowmeter was engineered with a patented design and built with corrosion-resistant PFA wetted material, the ideal solution for measuring aggressive acids and alkalis in chemical and industrial processes. Housed in a durable stainless-steel enclosure, the CIFM-88 is designed to withstand harsh industrial environments and meet IP65 and CE standards. A built-in 4-line LCD panel provides real-time data on flow rate, totalized flow, temperature and density.
Benefits of Coriolis flowmeters
Coriolis flowmeters offer several benefits compared to other types of flowmeters thanks to their operating framework. One key advantage is accuracy. Coriolis flowmeters provide the highest available measurement and control accuracy (±1%), thus ensuring the integrity and quality of a product batch, uptime and yield throughput.
Additionally, the accuracy of Coriolis flowmeters is unaffected by changes in fluid characteristics, such as density, viscosity and temperature. Other flowmeters can often struggle with fluctuations, leading to inaccurate measurements and, ultimately, batch inconsistency.
Another problem with non-Coriolis flowmeters is calibration requirements. With Coriolis flowmeters, frequent calibration is not necessary because fluid dynamics do not impact their accuracy. However, non-Coriolis flowmeters are susceptible to accuracy drops depending on fluid conditions. To counteract this, operators must calibrate their flowmeters when handling different fluids. If a variety of fluids are to be measured at different times, frequent calibration will take the flowmeter offline constantly, leading to costly, compounding downtime.
Versatility is another attribute exclusive to Coriolis flowmeters. When it comes to lower-viscosity fluids, traditional flowmeters tend to excel. But, if you put those same flowmeters, which include paddle wheel, vortex, differential pressure and ultrasonic, in intricate applications where viscosities are higher or viscosity dynamically changes during the process, their limitations become obvious.
For example, accurate flow measurement and control of slurry dispense in semiconductor polishing and lapping tools are critical to guarantee high throughput, reduced consumption and consistent quality. Diamond slurries are particularly difficult to measure due to their high viscosity, which can exceed 500 cP. Traditional flowmeters, such as paddlewheel and vortex meters, are not equipped to handle higher viscosities. Because Coriolis flowmeters are not impacted by varying viscosities, it makes them an ideal technology for this type of application.
Another benefit of Coriolis flowmeters is their ability to tolerate fluids that contain entrapped gases or bubbles. This may be a particular concern with slurries or solutions containing hydrogen peroxide. During measurement, Coriolis flowmeters can handle fluids with up to 30% bubbles. Traditional flowmeters are sensitive to the presence of entrapped gases, with ultrasonic models unable to operate past 5-10% of entrapped gases. The inability to measure fluids with these entrapped gas volumes leads to a loss of measurement accuracy and control, directly impacting process efficiency.
Conclusion
Flowmeters are essential technology for measuring the flow of fluids, gases and vapors, superseding traditional versions of this technology in applications with varying viscosities and characteristics.
The Coriolis flowmeter features a versatile principle allowing it to measure a wide range of fluids with high accuracy without performance setbacks. Its fluid measurement performance is independent of a fluid’s properties, eliminating the need for calibration when switching to different fluids.
Accuracy is also unaffected by flow variations, meaning the flowmeter will still provide the same accuracy measurements under laminar or turbulent flow conditions. Even entrapped gases (up to 30%) are unable to impact the performance of a Coriolis flowmeter. The versatility and superior accuracy of this technology deliver unparalleled performance in an abundance of challenging applications across growing industries.
Jay Rajagopalan | Sr. Director of Engineering and Product Management for Malema
Jay Rajagopalan is the Sr. Director of Engineering and Product Management for Malema. Malema is a product brand of PSG, a Dover company. PSG is the global pump, metering and dispensing-solution expert, enabling the safe and efficient transfer of critical and valuable fluids that require optimal performance and reliability in applications where it matters most. Additionally, PSG is a leading provider of flow meters designed to reduce waste and downtime while accurately measuring, monitoring and controlling the distribution of fluids.