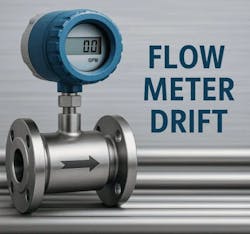
Flowmeters are precision instruments designed to measure the flow of liquids or gases through a system. Over time, however, even the most well-engineered flowmeters can begin to deviate from their original performance specifications, a phenomenon known as flowmeter drift. This gradual change in measurement accuracy can compromise product quality, increase operating costs and lead to compliance issues in regulated industries.
In this article, we will break down the most common causes of flowmeter drift, how to detect it and strategies you can use to minimize its impact over the life of your instrumentation.
What Is flowmeter drift?
Drift refers to a slow, unintentional change in the output of a flowmeter that is not due to changes in the actual flow rate. It is often observed as a progressive deviation from a known calibration standard or baseline measurement.
Unlike a complete sensor failure, drift is subtle and progressive, making it harder to detect until the discrepancy becomes significant. The key challenge is that a flowmeter can continue to produce consistent (i.e., repeatable) readings even as it becomes inaccurate due to drift.
Common causes of flowmeter drift
Understanding what causes drift is the first step toward preventing and correcting it. Here are some of the most common culprits:
1. Wear and tear of moving parts
In mechanical flowmeters, such as turbine or positive displacement (PD) meters, moving parts are subject to friction, erosion and fatigue. Over time, components such as bearings and rotors may wear out, altering the meter’s response to flow.
- Turbine meters, for example, can experience changes in rotor speed due to worn bearings, leading to inaccurate readings.
- PD meters may lose tight tolerances due to internal component wear, affecting volumetric measurement.
2. Fouling or contamination
The buildup of debris, scale, or biological matter can interfere with the flow path or sensing elements.
- In electromagnetic meters, mineral scaling on electrodes can reduce signal strength.
- In ultrasonic meters, air bubbles, solid particles, or coatings on transducers can interfere with wave transmission.
- Turbine meters may become sluggish due to sludge or particulate accumulation in the rotor assembly.
Fouling is especially common in applications involving dirty fluids, high solids content, or bioactive environments (like wastewater or food processing).
3. Temperature and pressure effects
Extreme or fluctuating temperature and pressure conditions can affect material properties and sensor electronics, leading to drift.
- Thermal expansion can affect the geometry of internal components, slightly altering flow paths.
- Pressure fluctuations may affect diaphragm or vortex elements, particularly in sensitive or low-pressure meters.
- Electronic components in some sensors (e.g., differential pressure transmitters) can experience drift due to prolonged exposure to heat.
4. Aging of electronics
Over time, the electronic components inside flowmeters, such as signal processors, capacitors and resistors can degrade. This can subtly change the response characteristics of the meter and alter calibration curves.
This kind of drift is typically gradual and more common in meters that operate continuously or under high electrical loads.
5. Changes in fluid properties
Flowmeters are often calibrated based on the expected properties of a fluid, such as density, viscosity or conductivity. If these properties change (due to seasonal variation, process change or contamination), measurement errors can occur.
For example:
- An electromagnetic meter calibrated for high-conductivity liquids might drift if used with low-conductivity fluids.
- Coriolis meters are sensitive to changes in fluid density.
- Turbine meters rely on predictable flow dynamics, which vary with fluid viscosity.
How to detect flowmeter drift
Drift detection is critical to maintaining long-term measurement integrity. Here are several methods:
1. Routine calibration checks
The most direct method is to compare the meter’s output to a trusted reference under known conditions. If discrepancies grow over time, drift is likely occurring.
2. Comparative metering
In systems with multiple flowmeters in series or parallel, comparing readings can help identify drift, especially if one meter begins to consistently differ from others.
3. Process trend analysis
Monitoring flow trends over time can highlight unexpected deviations that are inconsistent with operational inputs. A sudden change in flow rate without a corresponding process change may indicate drift.
4. Alarm tolerances
Some systems allow for the setting of upper/lower alarm limits. If a flowmeter frequently triggers these alarms without a real change in process, drift may be occurring.
Managing and preventing flowmeter drift
While some drift is inevitable over long periods, there are ways to minimize its impact and extend the life of your flow meter’s accuracy.
1. Schedule regular calibration
Routine calibration is the most effective way to correct for drift. The appropriate calibration interval depends on the application, fluid type and meter technology, but common intervals range from six months to two years.
For high-precision applications (such as custody transfer, pharmaceutical dosing or fuel measurement), shorter calibration intervals are recommended.
Tip: Choose a meter that allows easy recalibration or supports field calibration in-place (e.g., with a master meter or portable calibrator).
2. Choose the right meter for your application
Selecting a meter that’s appropriate for your fluid properties and process environment helps prevent drift from developing prematurely.
- Use non-contact meters (e.g., ultrasonic or electromagnetic) for dirty or corrosive fluids to avoid mechanical wear.
- For viscous or abrasive fluids, avoid delicate internal mechanisms.
- In temperature-variable environments, opt for meters with temperature compensation features.
3. Protect against fouling
Install upstream filters, strainers or separators to reduce the likelihood of particulates or contaminants entering the meter. Regular flushing and cleaning protocols can also help prevent buildup.
In bioprocessing or food applications, clean-in-place (CIP) systems should be designed to include flowmeters as part of the cleaning circuit.
4. Stabilize process conditions
Keeping temperature, pressure and flow rates within the meter’s specified range helps minimize measurement variability and electronic drift. Avoid sudden surges, water hammer or vacuum conditions that could stress components.
5. Monitor diagnostics
Modern digital flowmeters often come equipped with self-diagnostics that monitor internal status and signal integrity. These can provide early warnings of performance degradation or impending drift.
When to replace a drifted flowmeter
While regular maintenance can mitigate most drift, there are situations where replacement is the better option:
- The meter requires frequent recalibration to stay within spec.
- Replacement parts (e.g., bearings or sensors) are no longer available.
- The meter’s drift impacts quality, compliance, or profitability.
- Newer meter technologies offer better long-term stability.
Conclusion
Flowmeter drift is a reality for virtually all measurement technologies, but it doesn’t have to compromise your process. With an understanding of what causes drift, how to detect it and how to manage it through calibration, maintenance and smart meter selection, you can ensure your flow data remains accurate and reliable over time.
Whether you are measuring hydrogen fuel for custody transfer, dosing chemicals in a cleanroom or monitoring DEF levels in a fleet application, being proactive about flowmeter drift can save time, money and headaches down the road.
Mark Weiss | Marketing Specialist, Turbines, Inc.
Mark Weiss is a marketing specialist at Turbines, Inc.