P.I. Process Instrumentation's 2023 Innovation Awards winners
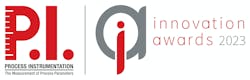
For more than 20 years, P.I. Process Instrumentation’s annual Innovation Awards program has recognized the latest solutions in process instrumentation. The program accepts nominations from companies that would like to submit their technology breakthroughs in process instrumentation. We would like to thank everyone who participated in the awards program by nominating. And, congratulations to this year’s winners. We hope to see your solution nominated next year. The following highlights the technology solutions from the 2023 Innovation Awards winners.
Endress+Hauser
Micropilot FMR63B
The Micropilot FMR63B offers many benefits to companies in the life sciences and food and beverage industries. The sensors also enable higher productivity levels, are easy to operate and offer increased product safety. The new Micropilot FMR63B level sensor satisfies all user requirements. In addition, thanks to innovative Ethernet-APL communication technology, the radar sensor ensures that process plants are ready for digitalization.
Companies in the life sciences and food and beverage industries are very exact regarding level sensors because hygienic applications are subject to the strictest compliance requirements, and precision and efficiency are key factors. The new non-contact Micropilot FMR63B radar sensor satisfies these requirements for liquids and solids. Non-contact level measurement with radar technology is now an established measuring technology, giving users an accurate overview of levels at all times without encountering the medium.
Furthermore, thanks to the verification technology, assurance the instrument electronics are operating within factory specifications can be confirmed without interrupting the process. Traceable verification enables increased product safety and guarantees conformity with compliance regulations.
The Micropilot FMR63B is for free space applications up to 80m and offers high beam focusing for vessels with many internal fittings as well as the following:
· Process connections: M24 adapters and hygienic process connections.
· Temperature: –40 to +200°C (-40 to 392°F).
· Pressure: –1 bis +25 bar (-14.5 to +362.6 psi).
· Maximum measuring range: 80 m (164 ft).
· Accuracy: ±1 mm (0.04 in).
· W-band: 80 GHz.
· EHEDG, 3-A, ASME BPE, International explosion protection certificates, 5- or 10-point linearity protocol.
Holistically, the FMR63B provides the following benefits:
· Fulfills highest compliance requirements of the industry.
· Easy handling through intuitive operation and wizards, for commissioning and verification.
· Increased productivity thanks to predictive maintenance and condition-based monitoring.
· Reduced downtime due to expanded diagnostic capability.
· Simple display of device status: change in the backlighting from green to red highlights errors immediately.
· Simple device integration into asset management systems through digital communication.
Siemens
FS-DSL Ultrasonic Flow Meter
Siemens Gas FS-DSL flow measurement system is a game changer in digital, non-intrusive, ultrasonic gas flow measurement — delivering, economical, high-performance gas flow measurement where power availability and/or footprint space are at a premium. Product highlights include:
Digital data: The Digital Sensor Link is a compact, externally mounted gas flow measurement system that converts analog transducer signals into digital data. The digital values and performance data are sent to the existing remote terminal unit (RTU) via Modbus at a rate of 100 times per second, providing fast, seamless and secure data acquisition.
Energy efficient: Providing the lowest power consumption (500-750mW) of any clamp-on flow measurement system, the FS-DSL is ideal for solar-powered remote installations, where higher power requirements would increase costs or prohibit a solar-powered option entirely.
Economical: Flexible design reduces cabling costs by allowing local or remote mounting. Less cabling also minimizes the chance for physical damage and RF interference on the Modbus digital interface.
Competitive advantage: The Gas FS-DSL arrives as a complete system, ready to interface into your customers’ RTU at a lower price than that of a standard system, making it one of the most competitive solutions for the gas market.
Swagelok Company
Swagelok Ammonia Sampler
Anhydrous ammonia is used in producing fertilizers, plastics, textiles, petroleum and more. To avoid ammonia stress corrosion cracking in storage tanks and product quality concerns, anhydrous ammonia is sampled to verify a water content of 0.2% to 0.5%. However, the manual sampling process can be dangerous.
The new Swagelok Ammonia Sampler makes anhydrous ammonia sampling safer by minimizing operators’ exposure to liquid and vaporized ammonia. It also introduces sampling consistency, significantly expedites the sampling process and eliminates the need to transport ammonia samples within facilities.
The first-of-its-kind Swagelok Ammonia Sampler addresses issues inherent to manual sampling by enhancing the following:
Safety: The sampler minimizes operator exposure to hazardous materials and environmental impact. Its glass-fixture design allows sample dispensing without exposing technicians, while allowing visual confirmation of process steps. This fixture design controls ammonia flashing into the environment. Because the sampler can be installed at the sample point, hazardous ammonia transportation through the plant is eliminated.
Accuracy: Manual processes can cause inaccuracies. The sampler delivers consistent results via a single-handle control, minimizing the chance of sampling errors. A pre-chilled residue tube allows for greater accuracy and prevents aggressive ammonia boiling. The sampler’s filling cold bath clears the supply line of older ammonia, ensuring fresh sample collections each time. The residue tube cap assembly prevents overfilling, keeping sample sizes consistent.
Efficiency: In manual sampling, it is difficult to fill a warm residue tube precisely because the ammonia boils off, which can take up to eight hours or more. The sampler produces results much quicker, enabling faster process adjustments to reduce rates of off-spec products and corrosion damage, lowering overall costs. The semi-automated sampler speeds sample collections and provides highly accurate results.
Emerson
Rosemount 3051 Pressure Transmitters
Rosemount 3051 Pressure Transmitters add new capabilities to the device that has been trusted by users for more than three decades. Powerful new features make the Rosemount 3051 easier to use, provide more insights and add diagnostic capabilities — all of which allows commissioning, maintenance and troubleshooting tasks to be completed faster.
The Rosemount 3051 delivers the same reliability and quality customers expect from Emerson, but now with modern features that help teams to be more efficient, facilities safer and overall operations more profitable. New features include:
· A larger, back-lit display is easy in all lighting conditions and ready to communicate in eight languages.
· Advanced display information like warning and error messages, you’ll see more actionable information on-screen.
· Visual icons give better insight to transmitter status for a more intuitive experience.
· Bluetooth Wireless Connectivity is a far simpler process to perform maintenance and service tasks without a physical connection or separate configuration tool. Communicate up to 10 times faster than traditional HART connections without removing covers, climbing tanks or scaffolding, or getting a hot work permit.
· User interface with task-based menus requires fewer clicks to access data and a common architecture across hosts and tools provide an identical experience regardless of how the device is accessed.
· Device led instructions for regular verifications, calibrations, and safety proof tests with a record of work saved to the device.
· Configure flow and level measurements all from one device.
· Identify hidden issues in the communication signal with loop integrity and identify plugged impulse lines that block accurate process readings.
· Track history with the diagnostic log to see all diagnostic events to help uncover intermittent issues.
Bell Technologies LLC
CENTER-TAP TORUS flowmeter
The CENTER-TAP TORUS (CTT) flowmeter was developed to achieve more precise flow measurement using basic laws of flow physics and address many limitations of differential-pressure type flowmeters that are currently used by the industry:
- This measurement method does not use fluid viscosity at flowing condition, hence it eliminates iterative calculation of flowing Reynolds number for discharge coefficient.
- Mechanically averaged monitored pressure reduces current minimum required meter run length.
- The Energy Correlation method of calculating flow rate eliminates the sharp edge of bore.
- The low-pressure being measured at the bore DP reading reduces fluctuations.
- Monitoring pressure at the bore allows placing downstream probe/transmitter closer to the meter.
- The Energy Correlation method of measurement is independent of viscosity, meter can measure flows in all flow regimes — laminar, transition or turbulent.
- Flow rate is defined by DP and flowing density only, meter output can be in mass or volume and meter can measure any fluid flow — drilling mud, wet gas, etc.
- Flow rate measured by monitoring DP at two sets of pressure taps, an operator can be alarmed when two readings differ beyond a predefined limit.
- Custom-designed meter can measure bi-directional flows.