Reimagining the instrument manifold for greater reliability
Manifolds are one of the hardest working pieces of equipment across the process industries. They are found in chemical, upstream oil and gas, and even food and beverage applications, where their ability to shut off or equalize pressure is an essential part of the process to keep a plant running efficiently.
However, traditional manifolds are often plagued with reliability issues, especially in applications involving fluids that are viscous or contain abrasive materials or grit, which can make them more difficult to operate. A manifold that gets plugged or has degraded over time can pose potential safety risks to not just the process but also to personnel.
Liability and reliability are of equal importance in any process, especially those that deal with abrasive or dangerous materials. Being able to efficiently and safely isolate, vent and equalize pressure within the system is why manifolds are an important piece of the equipment that could benefit from a better design.
Redesigning an instrument manifold to better meet the needs of operators dealing with challenging operations could ensure fewer process interruptions and more reliable readings, as well as a consistent product. A better manifold keeps process fluid from damaging the pressure transmitter while still ensuring it gives accurate pressure readings. By keeping fluid from negatively effecting the pressure transmitter, it, in turn, extends the life of the transmitter as well.
A better manifold
Designing an instrument manifold with wider bore channels further reduces the likelihood of clogging as it allows small sedimentary materials such as sand, grit or even sludge to flow through the manifold.
In the plant
In most instances, the pressure measurement is always being read. However, there are times when a valve needs to be closed or opened manually to redirect or stop the flow of process fluid to the transmitter — for instance, for scheduled transmitter maintenance.
Particularly challenging process flows of materials such as hot tar, maple syrup or peanut butter — to name a variety of the extremes — can build up and clog a manifold, especially if a bore channel is too narrow to accommodate the speed of the flow, which also affects the pressure that the meter registers. This buildup can then lead to an erroneous pressure measurement, which could cause the system to incorrectly compensate elsewhere in the process, possibly altering the flow, the pressure and, ultimately the end product.
In the field
Another area where instrument manifolds provide a valuable service is in fracking — the process of pumping a water and sand mixture into the ground to free up the oil and gas found in between shale plates. It is a tricky process that needs to be monitored carefully, ensuring that the right balance of water and sand goes in and closely watching the mixture that comes back up. The mixture pumped up from the shale plates will often have debris in it along with the oil and water — such as pebbles, sand and other gritty materials that can clog a manifold.
If too much other material comes up with the oil, including if the mixture has too much water, it might not need to go in the tank for oil but instead need to be pumped back into the ground as unusable. Similarly, if the pressure changes become too great from gas coming up with the oil and water mixture, it becomes critical to be able to release or equalize that pressure safely and avoid a blowout. Having a manifold that is easy to operate makes maintenance easier by simplifying transmitter isolation — ensuring that all measurement points are fully prepared and calibrated to handle any severe process conditions or sudden changes.
Cumbersome manifolds that require special tools or are uncomfortable to operate can contribute to decreased operational efficiencies and can potentially strain an operator's hand over time with continued use.
Using a better manifold
Looking at the drawings again, it becomes clear that a two-piece stem design with a non-rotating tip can make operations run more smoothly. The adjustable packing nut simplifies maintenance and allows for easier open-and-close operations. In addition, the stem and bonnet threads are fully isolated from the process fluid to minimize potential corrosion.
Keeping process fluid in the bore channel and away from the measurement sensor whenever possible ensures a longer life for equipment, especially in processes that have highly corrosive, sludgy or gritty materials in the flow.
A redesigned manifold that meets industry requirements is proving to be an asset to plants as they look for greater efficiency and reliability across processes.
Brandon Haschke is a product manager focusing on instrument manifolds for Emerson's Rosemount instrumentation business. He is currently focusing on helping operators in a variety of industries get the most out of their pressure measurement points. Haschke holds degrees in chemistry and chemical engineering from the University of Minnesota.
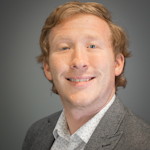
Brandon Haschke | Product manager focusing on instrument manifolds for Emerson's Rosemount instrumentation business
Brandon Haschke is a product manager focusing on instrument manifolds for Emerson's Rosemount instrumentation business. He is currently focusing on helping operators in a variety of industries get the most out of their pressure measurement points. Brandon holds degrees in chemistry and chemical engineering from the University of Minnesota.