Pressure measurement, Part 4: Differential pressure flow measurement
The previous article in this series paid homage to clever minds devising a way to measure a tank level through differential pressure. The final installment of this series will focus on using pressure measurement equipment to derive another process variable: flow. More specifically, measuring the flow rate of a fluid moving through a pipe.
This article explores the underlying physics, calculations and components involved in differential pressure flow measurement, one of the most common and versatile flow measurement techniques. Readers of this article will be able to make better-informed decisions when selecting differential pressure flow metering equipment for their specific applications. By understanding the principles and considerations of differential pressure flow measurement, readers can also gain insights into its significance and applicability in diverse industrial settings.
A brief history of flow measurement
The earliest known examples of flow measurement occur around the same time as the first written records in human history. Around 5000 B.C., ancient Sumerian cities near the Tigris and Euphrates rivers used flow measurement techniques to manage water flow through the aqueducts supplying their cities. The measurement technique used was rudimentary. A simple obstruction was placed in the water flow, and the amount of water flow was estimated by measuring the height of the water flowing over the top of the obstruction.
Fast forward to the era of modern physics. Scientific breakthroughs in the 1700s by Swiss mathematician Daniel Bernoulli and Italian physicist Giovanni Battista Venturi ushered in more advanced flow measurement principles using differential pressure. In 1738 Bernoulli published his seminal work, Hydrodynamica. In it, he introduces the concept of energy conservation of fluid flows. Bernoulli determined that the total energy of a fluid system remains constant. Therefore, a flow constriction causing an increase in the fluid velocity also causes a drop in the static pressure of the flowing fluid. This concept is the basis of differential pressure flow metering.
More recently, breakthroughs in physics have led to flow metering technologies such as turbine, electromagnetic, vortex, Coriolis and ultrasonic. Each of these flow metering technologies has its place in process control. However, differential pressure flow measurement has the longest history and, depending on the industry, is the most common method of measurement flow. So, let's explore the physics behind differential pressure flow metering more closely.
Calculating differential pressure flow
As mentioned, differential pressure flow meters work based on the principle of Bernoulli's equation, which states that the total energy of a fluid remains constant as it flows through a pipe. The following equation represents the conservation of energy principle applied to fluid flow:
P + (1 ⁄ 2) ρv² + ρgh = constant
where
P represents the fluid pressure
ρ represents the fluid density
v represents the fluid velocity
g represents the acceleration due to gravity
In a differential pressure flow meter, a constriction is placed in the pipe. This constriction reduces the area of the fluid path, increasing the fluid's velocity. Per the conservation of energy principle, this fluid velocity increase corresponds to a decrease in the fluid's pressure. The pressure difference between the upstream and downstream sides of the constriction is proportional to the square of the flow rate of the fluid.
Volumetric flow rate is determined through the following equation:
Q = C * A * √(ΔP / ρ)
where
Q is the volumetric flow rate of the fluid
C is a constant that depends on the geometry of the constriction and the fluid properties
A is the cross-sectional area of the orifice
ΔP is the differential pressure across the orifice
ρ is the density of the fluid
Primary, secondary and tertiary elements
A differential pressure measurement system typically comprises primary, secondary and sometimes tertiary elements.
Physical constrictions used to create a pressure drop in the flow stream are collectively known as primary elements. Primary elements all serve the same purpose of creating a measurable pressure differential in the flow stream, but they come in many different designs. These different designs serve a variety of purposes and applications. Examples of primary elements include orifice plates, venturi tubes, pitot tubes, flow nozzles and wedge meters.
The secondary element is the component that measures the pressure differential created by the primary element and converts it into a usable signal for determining the flow rate. Examples of secondary elements include differential pressure transmitters, manometers and pressure gauges.
The tertiary element is the component that receives the signal from the secondary element and provides the final output, a flow rate measurement. Examples of tertiary elements include flow computers, PLCs and other data acquisition systems.
However, it should be noted that modern differential pressure transmitters typically can perform flow rate calculations such as square root extraction. With these modern transmitters, it may be simpler to view the differential pressure measurement system as just comprising primary and secondary elements.
All of these elements are needed for a properly functioning differential pressure measuring system. However, the primary element is often overlooked in relation to the differential pressure transmitter. And in fact, primary elements have far more options, configurations and complexity. So typically, there is much more confusion surrounding them.
Primary elements vary in geometry and methodology of pressure drop creation. Selecting the right primary element is crucial for obtaining an optimal differential pressure flow measurement. The most suitable primary element for a particular application depends on several factors, including fluid type, line size, fluid temperature and pressure, solids content and many other variables. Figure 4 provides selection guidance for the most common primary elements: orifice plates, venturi tubes, flow nozzles, pitot tubes and wedge meters.
While much attention has been paid to improvements in differential pressure transmitters, primary element manufacturers have also made impressive innovations. The most notable innovation being integrated primary elements. Integrated primary elements combine the primary and secondary elements into a more streamlined device. Often these devices have internal pressure lines and a mounting area for a differential pressure transmitter. These innovations simplify installation and maintenance and also reduce potential leak points.
Square root extraction
Square root extraction, or square root scaling, is necessary to determine a flow rate using a differential pressure measurement. Differential pressure exhibits a non-linear relationship with flow rate. Square root extraction enables accurate flow measurement by establishing a linear relationship between the square root of differential pressure and flow rate (Figure 5). This linear relationship facilitates accurate flow rate measurement, increases instrument rangeability and improves noise immunity.
Previously, this scaling only took take place in the control system. But improvements in differential pressure transmitters have led to this scaling being available in the transmitter as well. So where should the square root extraction be performed? Either location is suitable; however, the conversion must occur once and only once. Excluding the conversion will lead to an error in the flow rate measurement, but doubling the conversion will also produce a significant measurement error. So, establishing a plant-wide standard specifying where the square root extraction will be performed is paramount. Once established, it should be documented and communicated to all personnel.
Another consideration for square root extraction is density-compensated mass flow measurement. Compressible fluids such as gases and steam often experience changes in their density. Volumetric flowmeters cannot account for these changes and will produce an inaccurate flow measurement. In density-compensated mass flow measurement, temperature and pressure measurements are used to calculate fluid density. This fluid density is combined with the volumetric flow rate to calculate a mass flow rate. These density-compensating calculations should always be performed before the square root extraction is performed.
Advantages and disadvantages
Over the past few decades, there have been significant advancements in existing flow metering technologies and the introduction of several new flow metering technologies. Some of these technologies cater to specific industries and applications, while others are more versatile. And while every flow metering technology has its merits and limitations, the intended application will ultimately have the most significant influence over the most suitable technology.
Key advantages of differential pressure flow metering technology:
- Simple and robust construction; no moving parts.
- Relatively inexpensive compared to other flow measurement technologies.
- Capable of metering gases, liquids and steam.
- Multivariable models can provide a compensated mass flow rate.
- Capable of measuring bi-directional flow.
Key disadvantages of differential pressure flow metering technology:
- Relatively high permanent pressure drop. Dependent on the type of primary element used.
- Limited rangeability compared to other flow metering technologies.
- Interference with the flow stream.
- Primary element will wear over time.
- Requires unobstructed upstream and downstream straight piping lengths. Dependent on the type of primary element used.
Overall, differential pressure flow metering is a widely used and cost-effective technique for measuring fluid flow rates in a variety of industrial applications. However, it is important to consider the advantages and disadvantages of this technique when selecting a flow meter for a particular application.
Conclusion
Flow measurement dates back to ancient civilizations but has evolved significantly over the past few centuries. Modern physics, particularly the work of Bernoulli and Venturi, introduced and refined the concepts of energy conservation of fluid flows and differential pressure flow measurement. Differential pressure flow measurement is now one of the most common and versatile methods of flow metering.
Differential pressure flow measurement offers many advantages, such as simplicity, cost-effectiveness, versatility in measuring various fluids and the ability to measure bi-directional flow. However, it also has disadvantages, including a permanent pressure drop, limited rangeability, potential interference with the flow stream and the requirement for unobstructed piping lengths. Understanding the advantages and disadvantages of differential pressure flow metering is essential for selecting the most suitable technology for specific industrial applications.
Ryan Bennett is a Marketing Manager for Azbil North America, based in Denver, Colorado. He holds a B.S. in Industrial Distribution from the University of Alabama at Birmingham. Ryan has worked in various roles at Azbil North America, with a current focus on product management and marketing. He can be reached at [email protected].
Azbil North America
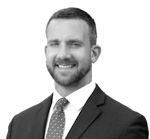
Ryan Bennett | Product marketing manager
Ryan Bennett is a product marketing manager for VorTek Instruments in Longmont, Colorado. He holds a B.S. in industrial distribution from the University of Alabama at Birmingham. Bennett has had a strong focus on steam metering, control and distribution throughout his career. He has worked in various roles at VorTek Instruments, with a current focus on new product development and marketing. Bennett can be reached at [email protected].